Die Casting Process Optimization Techniques
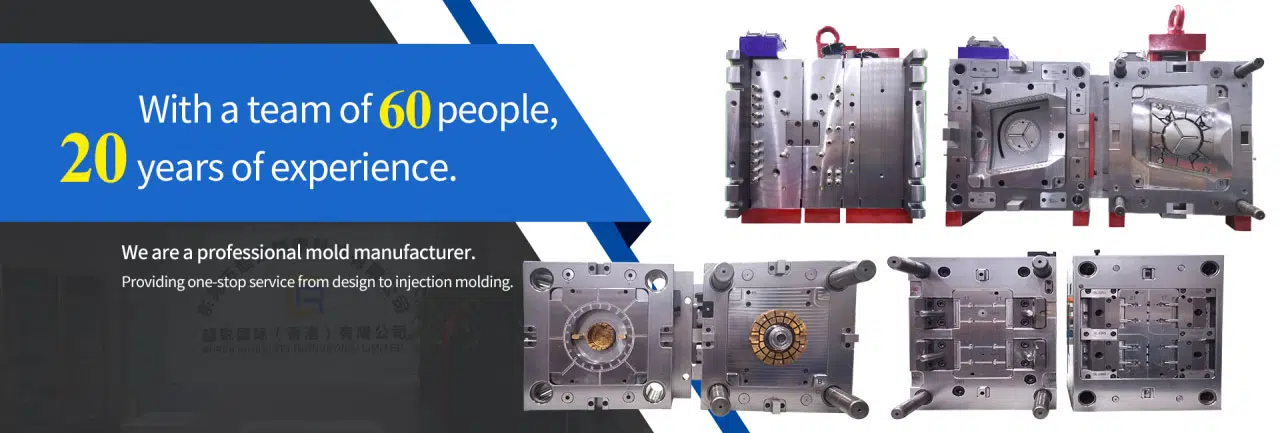
,文章长度约1000词左右
# Die Casting Process Optimization Techniques
## Introduction to Die Casting
Die casting is a manufacturing process that produces accurately dimensioned, sharply defined, and smooth or textured-surface metal parts. It involves forcing molten metal under high pressure into reusable steel molds, called dies. The die casting process is widely used across various industries due to its ability to produce complex shapes with high precision and excellent surface finish.
## Understanding the Die Casting Process
The die casting process consists of several key steps:
1. Clamping: The two halves of the die are securely closed by the die casting machine
2. Injection: Molten metal is injected into the die under high pressure
3. Cooling: The metal solidifies within the die
4. Ejection: The die opens and the casting is ejected
5. Trimming: Excess material is removed from the casting
## Key Optimization Techniques
### 1. Die Design Optimization
Proper die design is crucial for optimizing the die casting process:
– Implement proper gating system design to ensure smooth metal flow
– Optimize runner and gate sizes to minimize turbulence
– Design adequate venting to allow air escape
– Consider thermal management in die design
– Implement proper cooling channel placement
### 2. Process Parameter Optimization
Careful control of process parameters can significantly improve quality and efficiency:
– Injection pressure optimization (typically 1,500-25,000 psi)
– Proper metal temperature control (varies by alloy)
– Optimal die temperature management
– Injection speed adjustment
– Proper timing for each phase of the cycle
### 3. Material Selection and Preparation
Choosing the right alloy and preparing it properly affects process efficiency:
– Select alloys with appropriate fluidity characteristics
– Implement proper metal treatment before casting
– Control alloy composition consistency
– Use high-quality raw materials
– Consider secondary alloy additions for specific properties
### 4. Advanced Simulation Techniques
Modern simulation tools can significantly optimize the process:
– Flow simulation to predict metal filling patterns
– Solidification analysis to identify potential defects
– Thermal analysis for die temperature management
– Stress analysis for die life prediction
– Virtual process optimization before physical trials
### 5. Automation and Process Control
Implementing automation improves consistency and efficiency:
Keyword: Die Casting
– Automated ladling systems for precise metal delivery
– Robotic part handling and trimming
– Real-time process monitoring systems
– Closed-loop control of critical parameters
– Automated quality inspection systems
## Common Challenges and Solutions
### Porosity Reduction
Porosity is a common defect in die castings that can be minimized by:
– Optimizing venting system design
– Controlling metal temperature precisely
– Implementing vacuum-assisted die casting
– Using proper injection parameters
– Considering squeeze casting techniques
### Improving Surface Finish
Better surface quality can be achieved through:
– Proper die surface preparation
– Optimal release agent application
– Controlling metal flow patterns
– Maintaining consistent die temperature
– Implementing proper ejection techniques
### Extending Die Life
Die longevity can be improved by:
– Proper die material selection
– Implementing effective die cooling
– Using appropriate die coatings
– Regular die maintenance
– Proper die preheating procedures
## Emerging Optimization Technologies
### 1. Vacuum-Assisted Die Casting
This technique removes air from the die cavity before injection, reducing porosity and improving mechanical properties.
### 2. Semi-Solid Die Casting
Using metal in a semi-solid state offers several advantages, including reduced shrinkage and improved dimensional accuracy.
### 3. High-Integrity Die Casting
Advanced techniques that combine multiple optimization approaches to produce near-net-shape castings with minimal post-processing.
### 4. Real-Time Monitoring Systems
IoT-enabled sensors and data analytics provide immediate feedback for process adjustments.
## Quality Control Measures
Effective quality control is essential for optimized die casting:
– Dimensional inspection using CMM or optical systems
– X-ray inspection for internal defects