Moldflow Simulation in Injection Molding Process Optimization
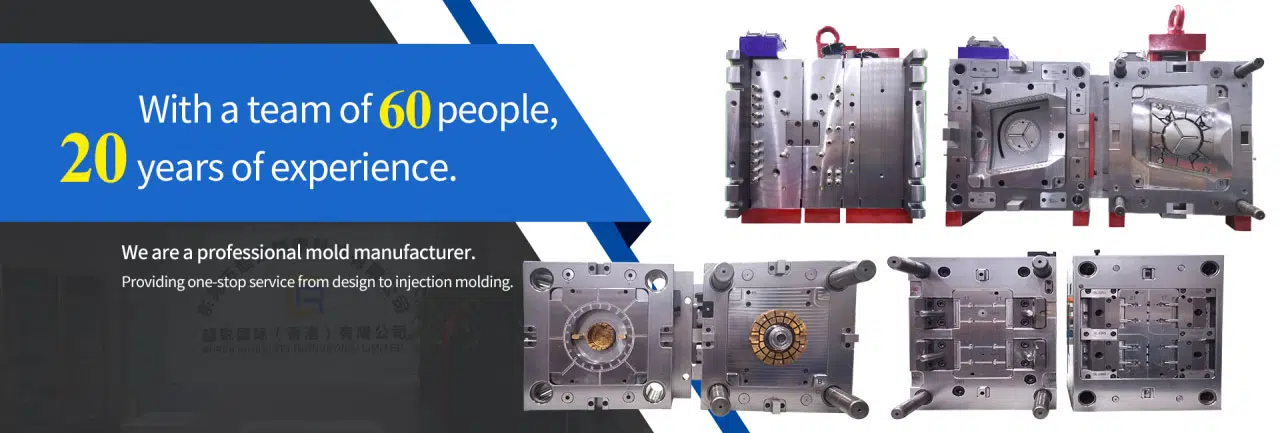
。
# Moldflow Simulation in Injection Molding Process Optimization
## Introduction to Moldflow Simulation
Moldflow simulation is a powerful tool used in the plastic injection molding industry to optimize the manufacturing process. By leveraging advanced computational techniques, engineers can predict and analyze the behavior of molten plastic during the injection molding cycle. This technology helps identify potential issues before physical production begins, saving time and resources.
## Key Benefits of Using Moldflow Simulation
The application of Moldflow simulation offers numerous advantages for injection molding optimization:
– Reduced development time and costs
– Improved part quality and consistency
– Minimized material waste
– Enhanced mold design efficiency
– Better prediction of potential defects
Keyword: Moldflow Simulation
## How Moldflow Simulation Works
Moldflow simulation software uses finite element analysis (FEA) to model the injection molding process. The software analyzes various factors including:
– Plastic flow behavior
– Cooling system efficiency
– Warpage and shrinkage
– Gate locations and filling patterns
– Stress distribution
By simulating these parameters, engineers can make informed decisions about mold design and process parameters before committing to expensive tooling.
## Common Applications in Process Optimization
Moldflow simulation is particularly valuable for:
– Optimizing gate locations and sizes
– Balancing multi-cavity molds
– Predicting and preventing sink marks
– Minimizing warpage and residual stresses
– Improving cycle times through cooling analysis
## Integration with Manufacturing Workflow
Modern Moldflow solutions integrate seamlessly with CAD software and manufacturing execution systems. This allows for:
– Direct import of 3D part geometries
– Automated mesh generation
– Real-time process monitoring
– Closed-loop optimization
– Data-driven decision making
## Future Trends in Simulation Technology
The future of Moldflow simulation includes:
– Cloud-based computing for faster analysis
– AI-assisted optimization algorithms
– Virtual reality visualization
– Integration with Industry 4.0 systems
– Enhanced material databases
## Conclusion
Moldflow simulation has become an indispensable tool for injection molding process optimization. By providing accurate predictions of molding behavior, it enables manufacturers to produce higher quality parts with greater efficiency and lower costs. As simulation technology continues to advance, its role in plastic manufacturing will only grow more significant.